The setting pressure value of the make-up relief valve is too high, resulting in fracture
補油溢流閥的作用是調節進入補油液壓系統的油量,并在不斷溢流的過程中保持控制系統壓力基本穩定。當系統中伺服液壓缸突然停止運動,而不需要油液時,補油溢流閥在標準設定壓力值時要能迅速地被打開,這就要求補油溢流閥要具有高的靈敏度,并且流量變化對壓力的影響要小。
The function of oil filling relief valve is to adjust the oil quantity into the oil filling hydraulic system, and keep the pressure of control system basically stable in the process of continuous overflow. When the servo hydraulic cylinder in the system suddenly stops moving and no oil is needed, the oil filling relief valve should be opened quickly at the standard set pressure value, which requires that the oil filling relief valve should have high sensitivity and the influence of flow change on pressure should be small.
因為三輪底盤攪拌車液壓泵在一直運轉供油,如果補油溢流閥靈敏度低而不能迅速地被打開,則控制系統中的油液就不能及時排出,壓力就會急劇升高,超過補油溢流閥的調整壓力,便會使補油系統各元件受力增加。在超調壓力作用下,伺服液壓缸活塞位移增加促使反饋桿轉動角加大。結果使反饋桿縮頸處與反饋閥套的尖邊相接觸,在超調壓力達到特定值時而導致反饋桿斷裂。
Because the hydraulic pump of the three wheel chassis mixer has been running to supply oil, if the sensitivity of the oil filling relief valve is low and cannot be opened quickly, the oil in the control system will not be discharged in time, and the pressure will rise sharply. If it exceeds the adjustment pressure of the oil filling relief valve, the stress on the components of the oil filling system will increase. Under the action of overshoot pressure, the increase of piston displacement of servo hydraulic cylinder makes the rotation angle of feedback rod increase. As a result, the necking part of the feedback rod contacts with the sharp edge of the feedback valve sleeve, and the feedback rod breaks when the overshoot pressure reaches a certain value.
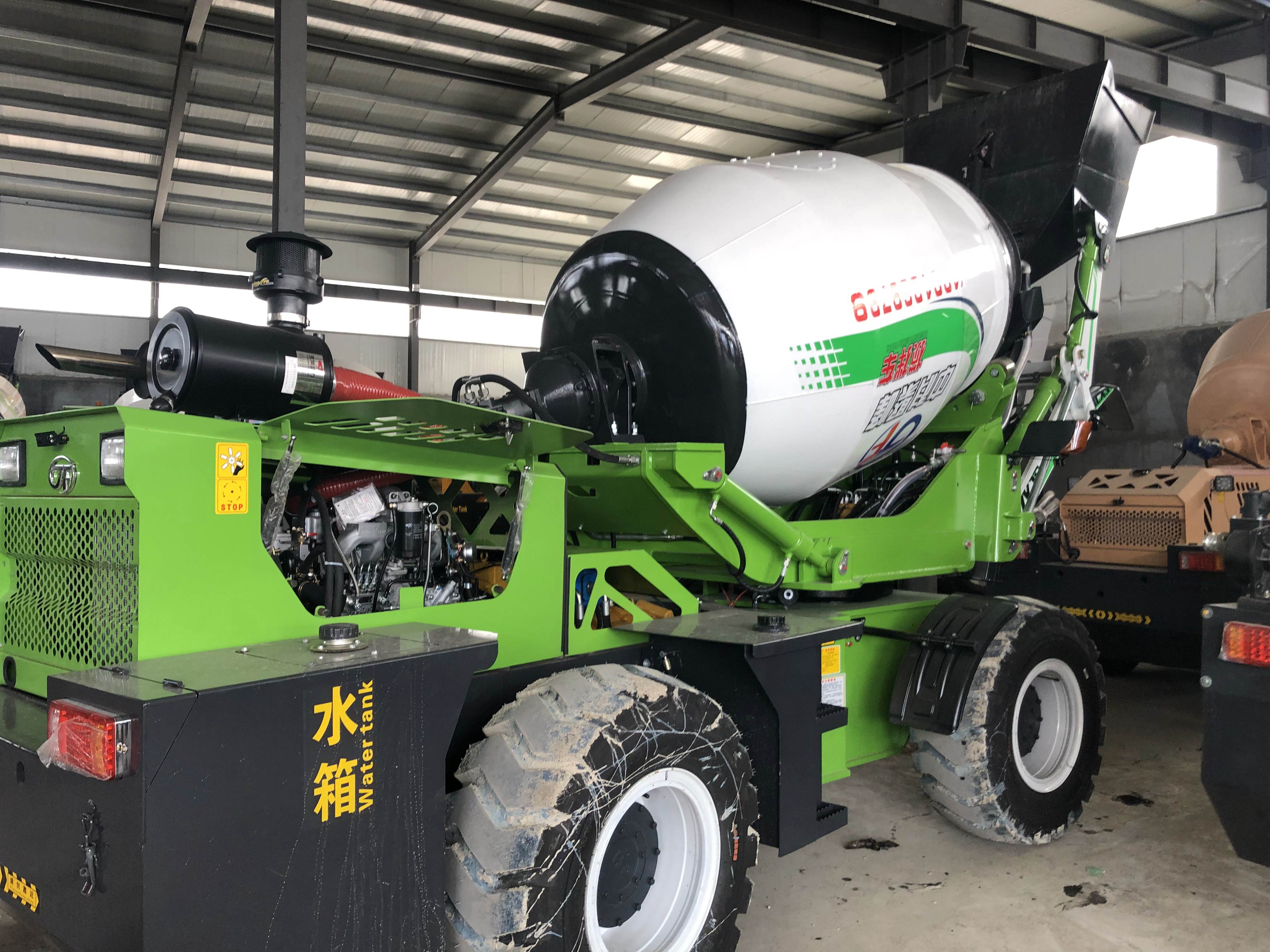
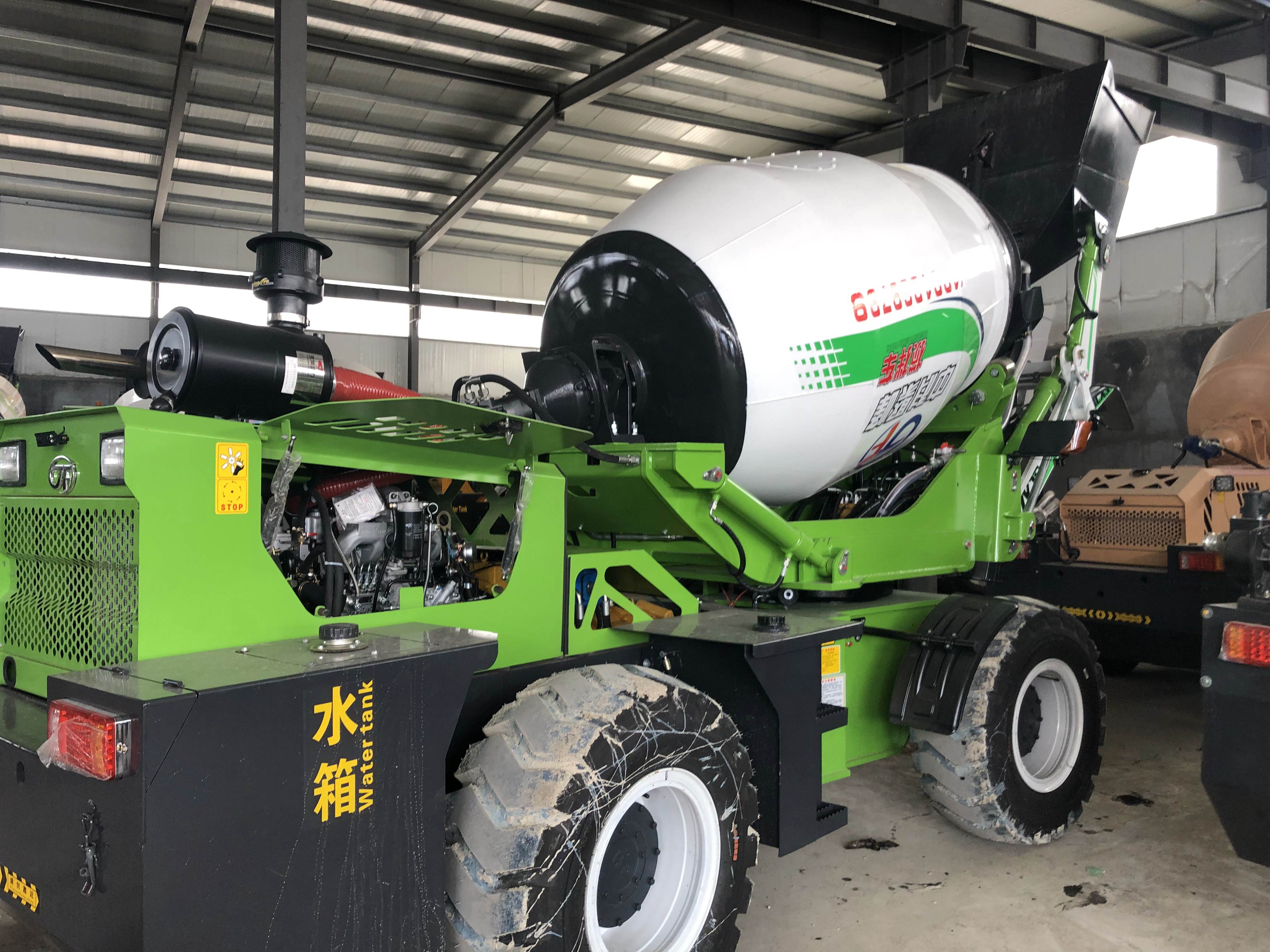
雙向彎曲疲勞導致斷裂
Fracture due to biaxial bending fatigue
金屬要斷裂,首先要形成微裂紋。三輪底盤攪拌車反饋桿實際上相當于一根擺桿,圍繞固定偏心轉軸瞬時,由伺服液壓缸活塞往復運動帶動反饋桿雙向擺動。反饋桿帶動反饋閥套動作而關閉控制油路并達到控制液壓泵斜盤角度,從而控制液壓泵排量的目的。
To break a metal, microcracks must be formed first. The feedback rod of three wheel chassis mixer is actually equivalent to a swing rod. Around the instantaneous center of the fixed eccentric shaft, the feedback rod is driven to swing in two directions by the reciprocating motion of the piston of the servo hydraulic cylinder. The feedback rod drives the feedback valve sleeve to close the control oil circuit and control the swash plate angle of the hydraulic pump, so as to control the displacement of the hydraulic pump.
反饋桿材料較薄弱的縮頸與桿身的交接處,由于尖角過渡在其桿身通向縮頸時產生應力集中。反饋桿縮頸與桿身的交接處在伺服液壓缸活塞和反饋閥套的作用力的反復作用以及與反饋閥套尖邊反復接觸下,疲勞微裂紋開始萌生并不斷擴展,之后導致雙向彎曲疲勞斷裂。
At the junction of the necking and the body of the feedback rod with weak material, due to the sharp angle transition, the stress concentration occurs when the body of the feedback rod leads to the necking. The interface between the necking of the feedback rod and the rod body is under the repeated action of the force between the piston of the servo hydraulic cylinder and the feedback valve sleeve, and under the repeated contact with the tip of the feedback valve sleeve, the fatigue microcracks begin to initiate and continue to expand, and then lead to bi-directional bending fatigue fracture.
沖擊作用加速疲勞斷裂
Impact accelerated fatigue fracture
液壓系統實際工作中,由于液壓泵容積的變化或者元件的某些缺陷,系統在輸出壓力油液時總是產生特定的振蕩。
In the actual work of the hydraulic system, due to the change of the volume of the hydraulic pump or some defects of the components, the system always produces a specific oscillation when it outputs the pressure oil.
再者,三輪底盤攪拌車進出料操縱換向裝置由于換向手柄推拉的一步到位,在突然換向或制動的時候,控制閥開關控制油路而對伺服液壓缸突然地供油或排油,但由于流動液體和運動部件具有慣性作用,突如其來的換向變化必然引起液壓系統瞬時壓力急劇變化而產生液壓沖擊。液壓振蕩或沖擊的結果使反饋桿和控制液壓缸活塞、反饋閥套尖邊發生反復碰撞而使反饋桿加速疲勞斷裂。
In addition, because the reversing handle is pushed and pulled in place, the control valve switch controls the oil circuit to supply oil or drain oil to the servo hydraulic cylinder suddenly when the reversing handle is suddenly changed or braked. However, the flowing liquid and moving parts have inertial effect, The sudden change of direction change will inevitably lead to the rapid change of instantaneous pressure of hydraulic system and produce hydraulic shock. As a result of hydraulic oscillation or impact, the feedback rod repeatedly collides with the piston of the control cylinder and the tip of the feedback valve sleeve, resulting in accelerated fatigue fracture of the feedback rod.